Yiyang Rubber & Plastics Machinery, Guilin Rubber Machinery and Fujian Tianhua under China National Chemical Equipment are important bases and backbone enterprises for rubber machinery R&D, manufacturing and export in China. They boast excellent technologies for tire curing presses that are exported to all parts of the world and widely used by a host of domestic and international tire manufacturers.
Since the spring this year, the rubber machinery enterprises have made achievements at home and abroad, with multiple curing press solutions adopted for a number of tire enterprises to build their digital, intelligent modern tire factories.
“Cloud model” for breaking down epidemic barriers
Recently, Yiyang Rubber & Plastics Machinery provided 16 sets of new 65-inch mechanical-hydraulic tire curing presses for the first overseas factory of a large domestic tire manufacturer. The curing presses were used to produce the first tire for the enterprise’s project with an annual output of 2 million all-steel radial tires.
Amid the epidemic, Yiyang Rubber & Plastics Machinery could not send technicians to the overseas plant to conduct on-site installation and commissioning, due to the heavy task completed in a short period of time. Yiyang Rubber & Plastics Machinery overcame multiple difficulties and gave online “face-to-face” technical guidance, with the matching of front and back offices. Through three months of efforts, the equipment was installed and commissioned as scheduled. YRPM save valuable time for the customer’s smooth production of its first tire. The Yiyang-based company will also have 16 sets of curing presses delivered to the tire manufacturer’s overseas plant.
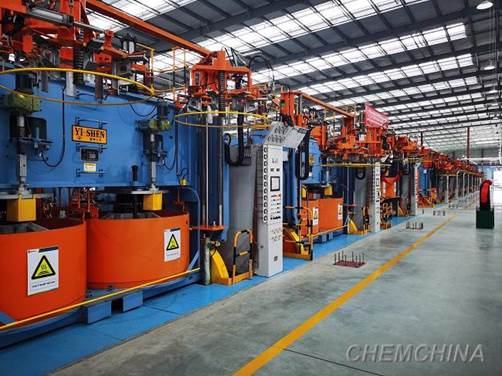
Yiyang Rubber & Plastics Machinery’s 16 sets of 65-inch new curing presses at the production site of customer’s overseas factory
Guiling Rubber Machinery has also leveraged the “cloud model” to break down COVID-19 barriers.
“Several new structures have been added to this equipment. Please look in the direction of my finger...”
In mid-March, Guilin Rubber Machinery’s members served as livestreamers using laptop computers and mobile phones to explain a new curing press respectively from the fixed and mobile perspectives. This all-steel hydraulic tire curing press, an important equipment for an overseas customer to develop new tires with special structures, has been customized and optimized by Guilin Rubber Machinery according to relevant requirements.
During the two hours of live broadcast, the overseas customer’s acceptance personnel implemented a strict inspection involving 3 major items and multiple minor items, such as the appearance, operating action and operation accuracy. They finally confirmed that all performance parameters met the requirements and that the acceptance was passed.
The pandemic remains severe, imposing difficulties for people to enter and leave the country. But the situation cannot beat the rubber machinery companies. Through exploration, one-stop barrier-free remote services have been offered, including online sales, communication, live acceptance, and remote installation, commissioning and support. By breaking down epidemic barriers via the “cloud model”, the rubber machinery enterprises are connecting with a growing number of customers from Bangladesh, Thailand, Pakistan, Turkey, and the United States.
Multi-size equipment for diversified needs
Through decades of R&D and efforts, the rubber machine enterprises have developed multiple series of solutions and curing presses with complete specifications and strong adaptability.
According to relevant data, Guilin Rubber Machinery, has relied on diversified tire production solutions, with the amount of new orders surging more than 400% year-on-year in the first quarter of 2021. A variety of models have gained favor of customers, including 2250 mechanical reinforced tire curing press, 1950 mechanical dual-mode tire curing press and 2665 mechanical tire curing press.
Regarding the 2250 model, the stress system and transmission device have been optimized to increase the mold-clamping force of curing press, which is more suitable for meeting the curing needs of special tires.
One 1950 mechanical dual-mode curing press can produce the same number of tires as two conventional 1950 mechanical single-mode curing presses, increasing the capacity per unit area by more than 25% and significantly reducing the investment of tire manufacturers’ infrastructure.
The 2665 mechanical curing press, a classic model of Guilin Rubber Machinery, has been tested in the market, featuring stable quality and high reliability. It can be used to cure all-steel radial engineering tires, bias engineering tires and agricultural radial tires with rims of 24"~51" diameter.
Also, the situation of Guilin Rubber Machinery’s overseas orders has been equally promising. The 1665 and 1630 mechanical dual-mode tire curing press will function in different overseas regions.
The 1665 model was ordered the most as an export project in the first quarter. This batch of equipment will be used in the production line of a digital factory with an annual output of 2 million all-steel radial tires. This model has the characteristics of high locating accuracy and short non-curing time, which can improve the production efficiency and output of tires.
The 1630 model, customized for US customers, has been designed for production lines for high-end all-steel truck tires. The highly automated equipment meeting relevant safety standards can be exported in bulk to the American market.
Yiyang Yishen Rubber Machinery Co., Ltd., a Sino-foreign joint venture under YRPM, has been committed to developing itself into a supplier offering customers high-quality cost-effective curing presses. Its curing presses are widely applied in all divisions of tire manufacturing. Currently, there are 30-odd specifications and models of hydraulic and mechanical curing presses. They can be designed and produced according to the customized needs.
“The value of a high quality vulcanizer will be more prominent over time,” said Yao Hongjian, YRPM's Party secretary, chairman and general manager. “In terms of after-sales services, YRPM has also provided customers with the most timely and perfected brand services, so that customers feel pleasant and reliable in their cooperation with YRPM.”
Helping transform and upgrade smart manufacturing of tires
During the 14th Five-Year Plan period, China will continue to improve smart manufacturing in the tire industry, which put forward higher requirements for highly intelligent integration of curing press.
Recently, two 1900 frame-type dual-mode hydraulic curing presses, developed by Guilin Rubber Machinery, were applied to produce tires in a large tire factory in China. They are a new model designed for meeting the requirements of innovating and upgrading smart manufacturing of tires.
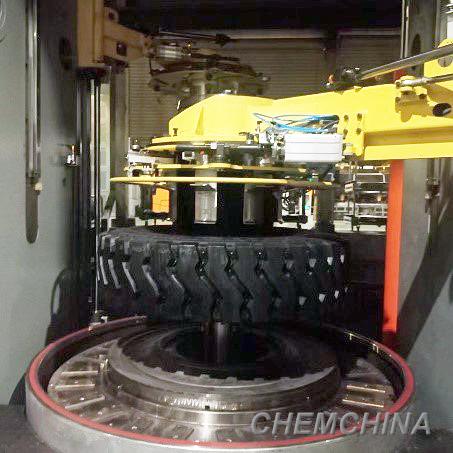
Guilin Rubber Machinery’s 1900 frame-type dual-mode hydraulic curing press is vulcanizing tires
The left and right dies of the new 1900 model are independently controlled, which can realize dual-mode vulcanization of tires of different specifications simultaneously. The mold-clamping force of this machine is evenly distributed, and the quality of produced tires is more stable. The new vulcanization chamber makes the sealing more reliable, and the service life of the sealing ring can reach more than 6 months. Fully automatic operation can be directly matched with unmanned vulcanization factories, facilitating the development of smart plants for tire manufacturers. The steam tube of this model is in the form of integrated valve group, saving 15% energy than the traditional one. It has been designed to facilitate a green, energy-saving and emission-reducing smart tire manufacturer.
To adapt to the fully automated production, Guilin Rubber Machinery, in collaboration with tire manufacturers, has tailored the layout of their curing press plants with due consideration to the intelligent operation. With the same floor area, the 1900 model can be used to produce more tires simultaneously, featuring strong adaptability, good safety and high efficiency.
According to the Guiding Outline of the 14th Five-Year Plan for the Development of Rubber Industry issued by China Rubber Industry Association, the meridian rate of tires in China should reach 96% during the 14th Five-Year Plan period. Guilin Rubber Machinery innovatively proposed the “hydraulic dual-mode engineering-tire curing solution” to realize the mass production of radial engineering tires.
Yiyang Rubber & Plastics Machinery and Fujian Tianhua are also speeding up their digital and smart development.
YRPM’s digital manufacturing base for smart rubber machinery is about to be completed. YRPM will work to meet the goal of developing itself from a digital enterprise to smart one.
With its fine manufacturing tradition, Fujian Tianhua is leveraging the lean management and advanced technologies epitomizing KraussMaffei’s new workstyle, building itself into a high-end smart machinery manufacturer for rubber & plastics products.
Facilitating our transformation and upgrading
Creating diversified solutions for equipment
Meeting the safe, efficient and green production needs of digital smart tire manufacturers
Empowering your future